A2M2X Post Show Report
See the highlights and statistics from our inaugural A2M2X event in October in Detroit!
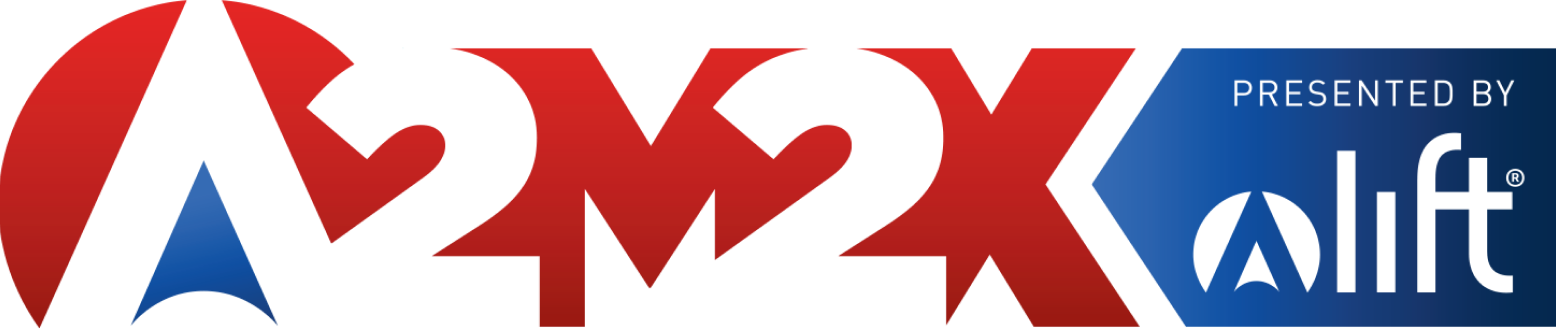
How LIFT Works
LIFT accelerates the adoption of new advanced manufacturing techniques and educational tools for industry and the Department of Defense by connecting industry, academia and government.
LIFT, and its ecosystem, designs, builds and tests, innovative materials, manufacturing processes and curriculum, moving the U.S. industrial base into the future.
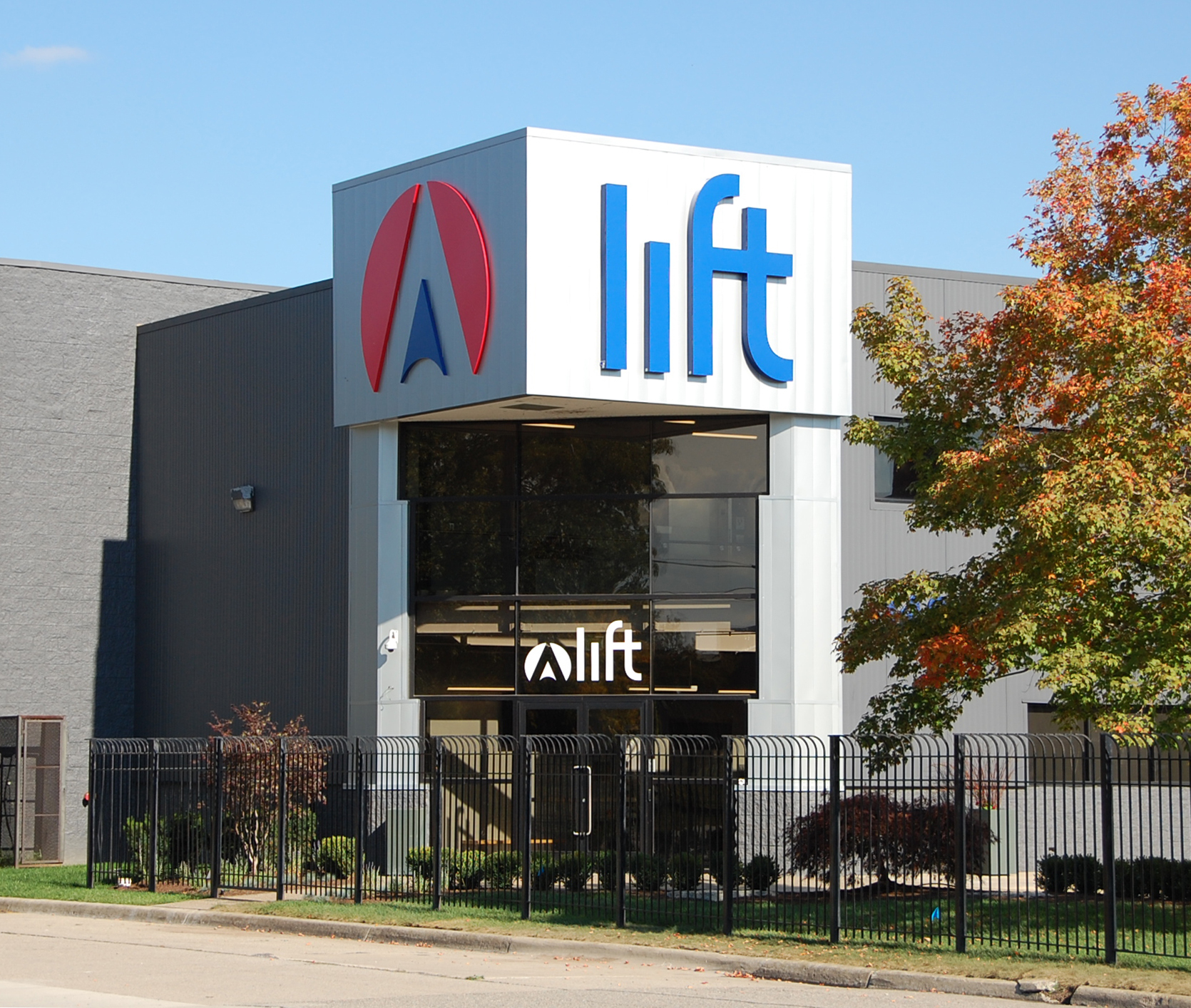
The LIFT Ecosystem
LIFT is a membership-based ecosystem committed to shaping the future of American advanced manufacturing.
From global companies and top national academic and research institutions to small & medium-sized manufacturers and start-up organizations, our members work in concert to position the United States as the global leader in advanced manufacturing.
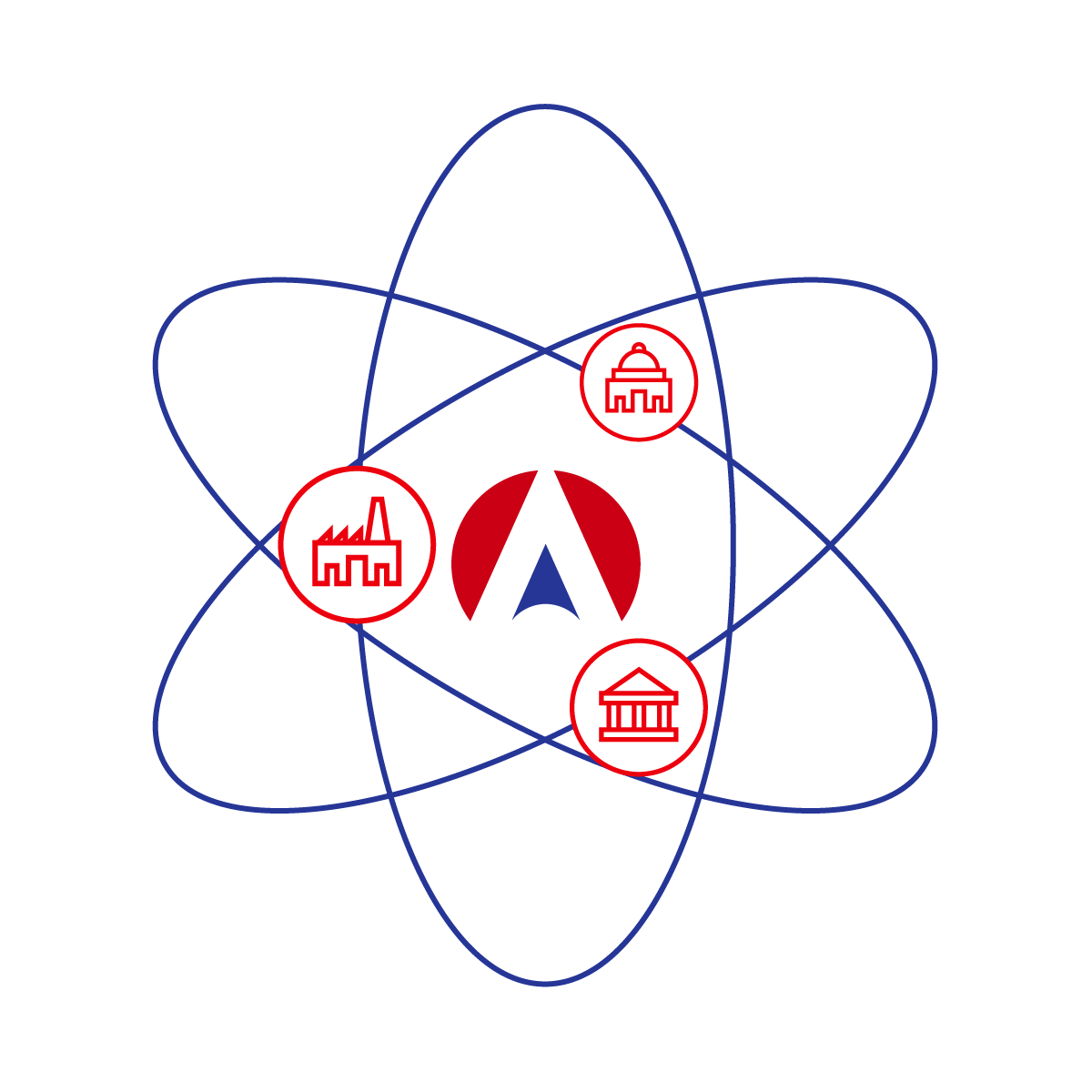
The LIFT Advantage
As a public-private partnership, LIFT harnesses the power of American industry, academia, and government to collaborate, accelerate, innovate and educate.